RF Batch Dryer
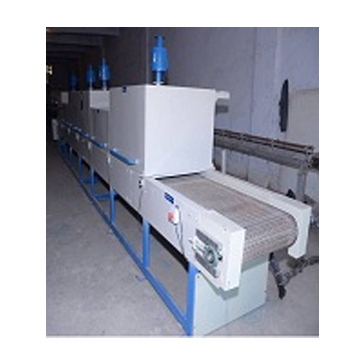
In radio frequency drying, material is exposed to an electronic field that alternates about 40,000,000 times per second. When the field alternates, the water molecules in the material also alternate. The resulting friction causes the water to heat uniformly throughout the product. Radio frequency drying can save energy because only the product itself is heated. Another benefit is that no equipment warm up or cool down is necessary. The technology typically replaces process steam heat.
The RF Web Dryer rapidly removes moisture from the web at low temperatures and prevents the migration of coating solids caused by conventional drying which increases web strength and product quality.
Benefits
- PREFERENTIAL HEATING: Selectively dries products at the wettest sections of the web. The product output will be uniform in moisture content throughout, regardless of the non-uniformity going in.
- INCREASES PRODUCTION THROUGHPUT: Providing instant ON/OFF control, the RF Web Dryer eliminates the heat-up and cool-down times required by conventional dryers. MINIMIZE DRYING TIMES: Rapid volumetric heating eliminates the long dwell time required by conventional heating minimizing the quantity of product in the drying cycle and reduces changeover time.
- NO ACCUMULATION ROLLERS: This dryer eliminates the need for accumulation rollers required by festooned convection and infrared type dryers and saves floor space by generally requiring one-fifth of the floor space needed for hot-air and IR dryers as well as lowering maintenance costs.
Features
- Energy applied by radio waves at a frequency of 40.68 MHz.
- Volumetric heating keeps the temperature low and uniform throughout the web to prevent overheating.
Barriers to Market Acceptance
- price
- risk of failure
- benefits not understood
- priorities not on benefits of new technology
- lack of technology awareness
Applications
Radio frequency drying is often used to dry crackers, cookies, and other snack foods after they've been baked. It can also be used to dry ceramics, synthetic foam, textiles, water-based inks and adhesives in paper products, and fiberglass yarn. Other applications include sterilizing bagged materials and preheating thermoset plastic molding compounds. Drying municipal sludge and timber is being investigated.