Rotary Retort Furnace
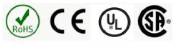
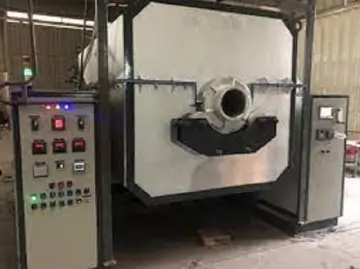
The Rotary Retort Furnace is an innovative industrial solution that is revolutionizing thermal processing in a variety of manufacturing industries. This modern furnace employs a rotating cylindrical retort to enable a range of heat treatment applications. It is built for maximum efficiency and adaptability. Its innovative design ensures even heating, resulting in dependable and superior performance in processes like as sintering, calcination, and pyrolysis.
Rotating retorts have been used to continually heat a variety of basic materials. Rotating retort furnaces are especially adaptable, allowing for controlled environment operation up to 500 °C. These furnaces are especially good for processing raw materials because the revolving conveying movement tumbles the materials, dislodging any jams or tangled clumps. This makes it possible to heat treat every single component more thoroughly. Uneven and unsuitable loading, parts jams that happen at the charge end and cannot be broken up in the retort, sealing and rotating bearing maintenance within the heated shell, and loss of regulated environment are issues with the traditional rotary retort concept.
The retort's circular motion, which enhances heat transmission and lessens material handling challenges, makes it a fantastic choice for businesses handling a range of sensitive commodities. The Rotary Retort Furnace is versatile enough to tailor its temperature and residence time characteristics to the unique requirements of different materials and processes.
Features
Advantages
- No special pit or foundation
- Low maintenance – maintenance is limited
- Flexibility – small or large production runs can be handled alternately or continuously; close control of furnace operation is easily obtained
- Automation – heat treating is completely automatic after loading raw materials into hopper
- Uniform loading – a specially designed vibratory hopper and weight-actuated skip loader deposit precisely measured charges into the furnace
Related images
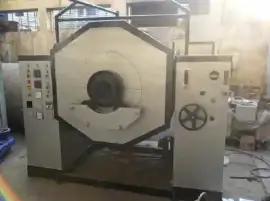
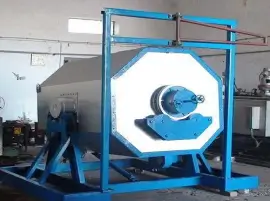